|
Plant Simulation |
|
|
【Plant Simulationとは】 |
Plant Simulationは、国内外の多くの製造業で幅広い実績があるDiscrete Event Simulation
(離散系シミュレーション)ツールです。
Plant Simulationは、生産シミュレータはコンピュータ上に仮想の工場ラインモデルを構築し、
物の流れを見える化することで様々な現象(生産、動き、渋滞、保管、輸送、サービス、エネルギー)を
検証・分析し、改善へとつなげるものです。 生産ラインをモデル化する標準オブジェクトライブラリに
加え、遺伝子アルゴリズムによる最適化エンジンやVSMといった先進機能を提供しており、
工場新設計画から既存工場の改善検討まで、複雑な生産ラインをモデル化し、高速にシミュレーションにすることができます。
Plant Simulation を使用することで、実際の工場や生産ラインを構築する前に、机上で高精度に工場の
モノと情報の流れを見える化して分析することが可能になり、物流や生産ラインのボトルネックを解消し、工場のKPIを最適化することができます。
中でもPlant Simulationは豊富なライブラリ群、強力なカスタマイズ機能、階層型モデリング等により、 いかなる規模の複雑な生産システムでも限りなく現実に近く再現し、高速にシミュレーションすることができます。
|
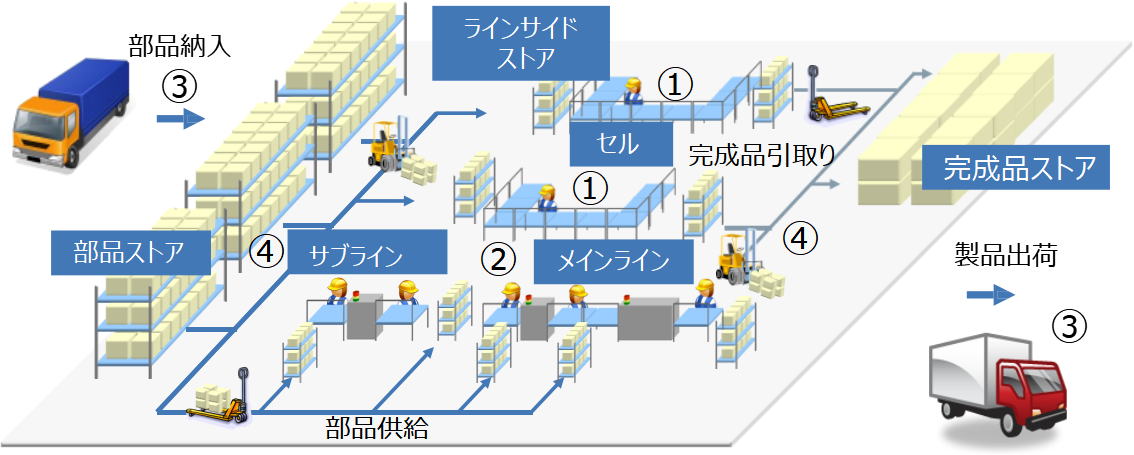 |
|
|
【Plant Simulation の特徴】 |
1.簡単なモデル作成・変更&複雑な工程の再現性 |
①階層構造
→目的の抽象化レベルでモデル化・シミュレーションが可能です。
段階的に詳細化することで、正確に、 且つ分かり易くモデル化いたします。 |
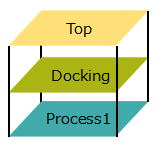 |
②ライブラリ管理
→独自のライブラリを作成した場合でもライブラリの管理機能にて、
バージョン管理が可能であるため、バージョン管理の手間を削減します。 |
③継承・ライブラリ
→オブジェクト指向の継承が使用可能のため、同一ラインの複製・同一 ラインの
調整分などが簡単にモデル化可能でき、モデル作成の時間を大幅に削減します。 |
|
|
2.高速なシミュレーション |
・1日、1週、1ヶ月、1年など生産期間を任意に設定し、
長期間のシミュレーション設定でも短時間で実行可能
・膨大な量になる工程改善の為の組み合わせ問題を高速に分析 |
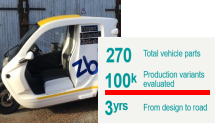 |
|
|
3.容易な工場モデリング |
・標準オブジェクトライブラリを利用して、オブジェクト
の配置とパラメータ設定をすれば基本的な
モデル作成が可能
・お客様固有の複雑な製造要件や制約をプログラミング
してユーザ固有オブジェクトを作成しモデルに組み込む
ことも可能 |
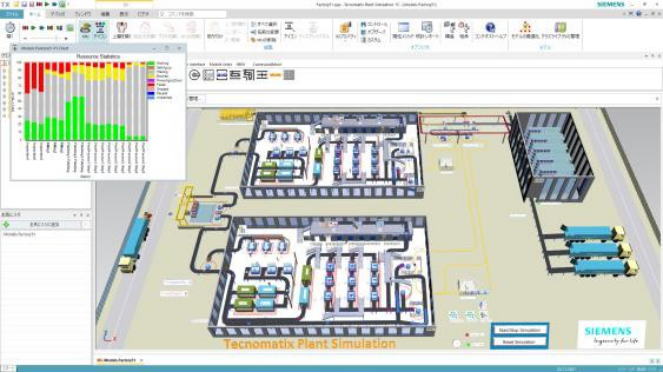 |
|
4.自動最適化エンジン |
・遺伝子アルゴリズム(GA)による自動最適化エンジン搭載
・スループットやコストなど達成したい「最適化の目的」と、
作業者数やバッファ量などの「最適化の対象」を設定する
ことで短時間で自動的に解を導出 |
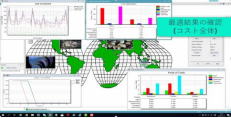 |
|
|
5.持続的な改善 |
・モデルに実工場の実績データ(在庫数、性能値)と、
計画(生産量、部材納入) を入力することで、
生産を最適化
・システム化することで、自動で持続的な改善が可能 |
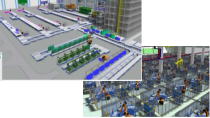 |
|
6.VSM*モデル |
・サプライヤへの発注から納品までをシミュレーション
・モノと情報の流れから、サプライチェーンと在庫の可視化、いつ、どこで、どの程度の
ムダが発生するかを分析し、ムダ削減
・オブジェクトの配置とパラメータの設定でモデルを容易に設定・変更可能
*)VSM:Value Stream Mapping、トヨタ生産方式で発案された、モノと情報のフローを明確化し、ムダを省く手法 |
|
7.チャートとサンキー |
・稼働率、バッファ容量など、シミュレーションで刻々と変化する状態量を分かりやすく
グラフィカルに表示
・物流導線と物流量の変化を表示 |
|
 |
|
|
【Plant Simulationを活用したSCMの検討・改善】 |
材料/部品在庫の計画把握・改善 |
|
材料/部品発注、仕掛在庫、納期の関係性 |
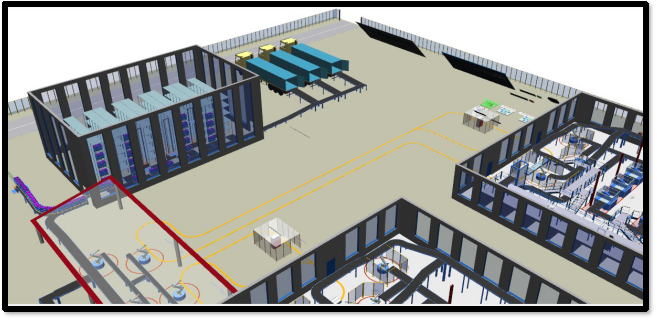 |
|
物と情報の流れ図:Value Stream Mapping |
◆現在の生産計画では材料が「どの時期に、
どの材料・部品がどれだけ必要かを把握
◆現状の在庫・納入計画で、
KPI(生産量、稼働率など)の 把握・改善 |
|
◆サプライヤへの発注から納品までを
シミュレーション
→現在の材料発注の時期・量で仕掛在庫・
稼働率・納期の確認 |
|
|
|
【材料/部品在庫の計画把握、改善】 |
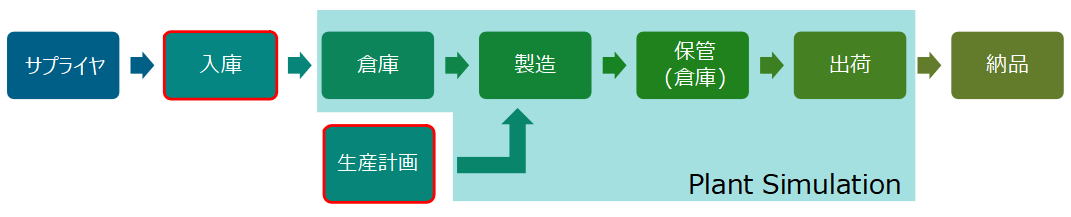 |
◆最適な納入計画の作成
・生産計画をInputとしてシミュレーション
・材料・部品については制限無し
*シミュレーション結果として、 「いつ」「どの材料・部品が」「どれだけ」 必要かを把握 |
◆既存計画の生産能力の把握
・生産計画をInputとしてシミュレーション
・材料・部品は納入計画をInputとしてシミュレーション
*シミュレーション結果として、今の納入計画の生産への影響を把握 ・全体生産量の把握 ・部品の過不足による
ボトルネック、過剰な仕掛在庫の把握 |
|
【導入から運用までの流れ】 |
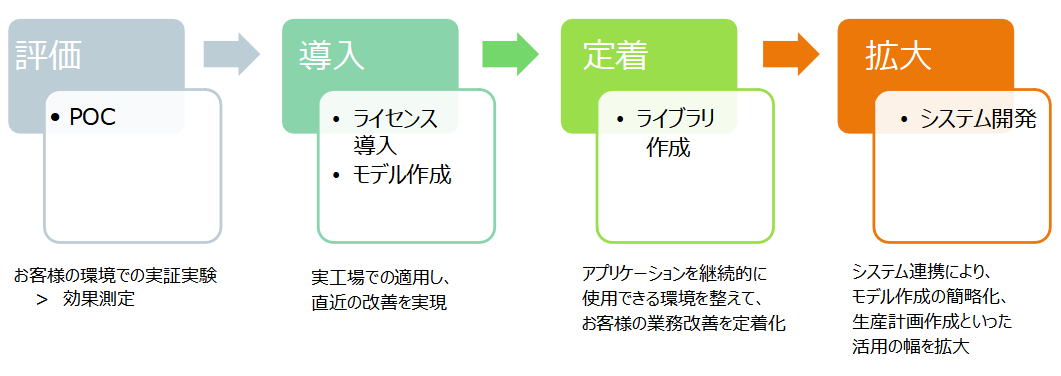 |
|
【Proof of Concept(概念実証)】 |
パターン①:トライアルライセンス+学習マテリアル |
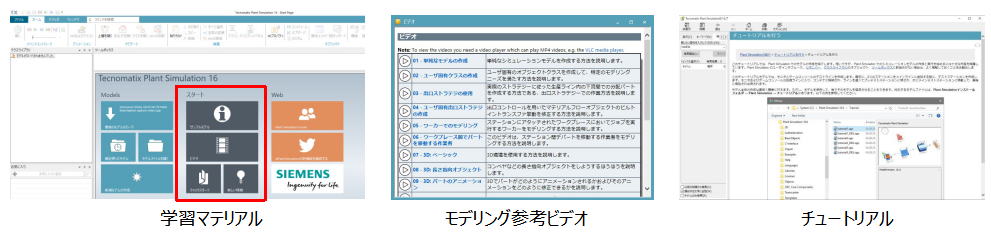 |
|
パターン②:有償トレーニング+トライアルライセンス
・3日間のトレーニング(基礎モデリング、プログラミング、Case Study) |
|
パターン③ :有償モデリングサービス + トライアルライセンス
・目的 :短期間でPlant Simulationを使用して、どんな改善が可能であるかを確認する
・有償モデリングサービス :お客様の工場を弊社で作成
・トライアルライセンス :弊社が作成したモデルを使用し、お客様で改善の検討 |
|
*Proof of Conceptパターン③:効果の確認
|
PoCの目的 |
|
PoCの進め方 |
|
・導入することによるメリットを推測
・デジタル化を進めるフローの把握
※データ作成の評価は含めず
|
|
有償モデリングサービス
+トライアルライセンス
・有償モデリングサービス
⇒お客様の工場を弊社で作成
・トライアルライセンス
⇒弊社が作成したモデルを使用し、
お客様で改善の検討 |
|
PoCでの確認事項 |
|
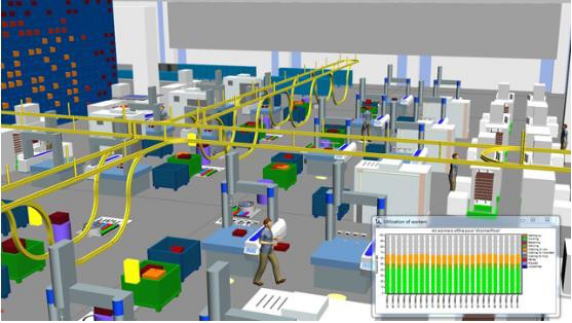 |
|
・シミュレーションで評価できるKPIの定義
・デジタル化に必要なデータの種類
・場所の確認
・シミュレーションによるKPIの把握
・シミュレーションを活用した改善フローの把握
・デジタル工場と実工場の差の比較 |
|
|
|
【Plant Simulation 導入フロー】 |
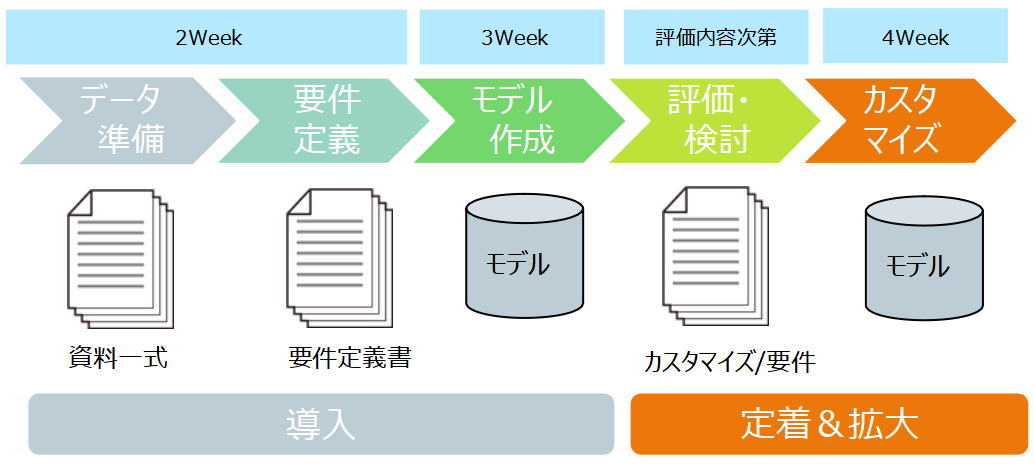 |
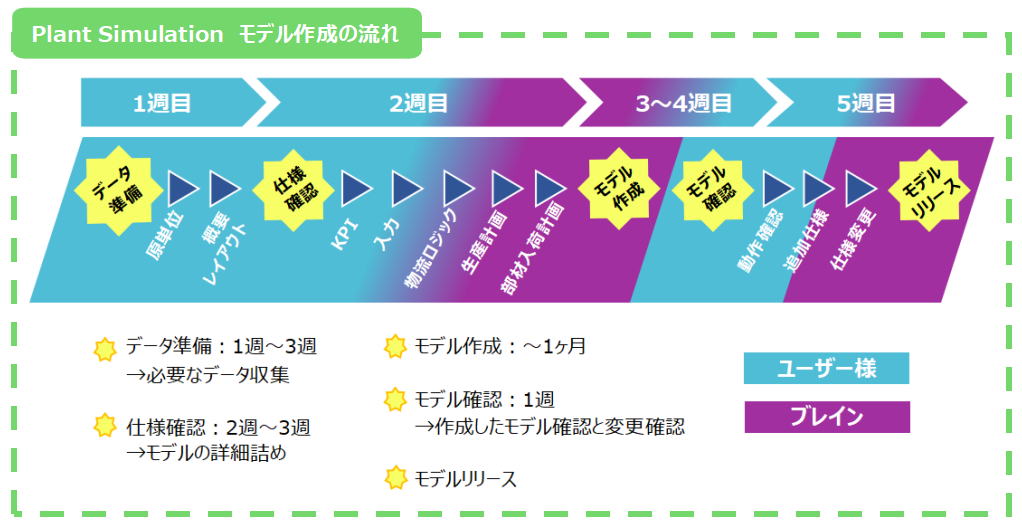 |
|
|
【幅広い業界での実績・効果】 |
◆実績◆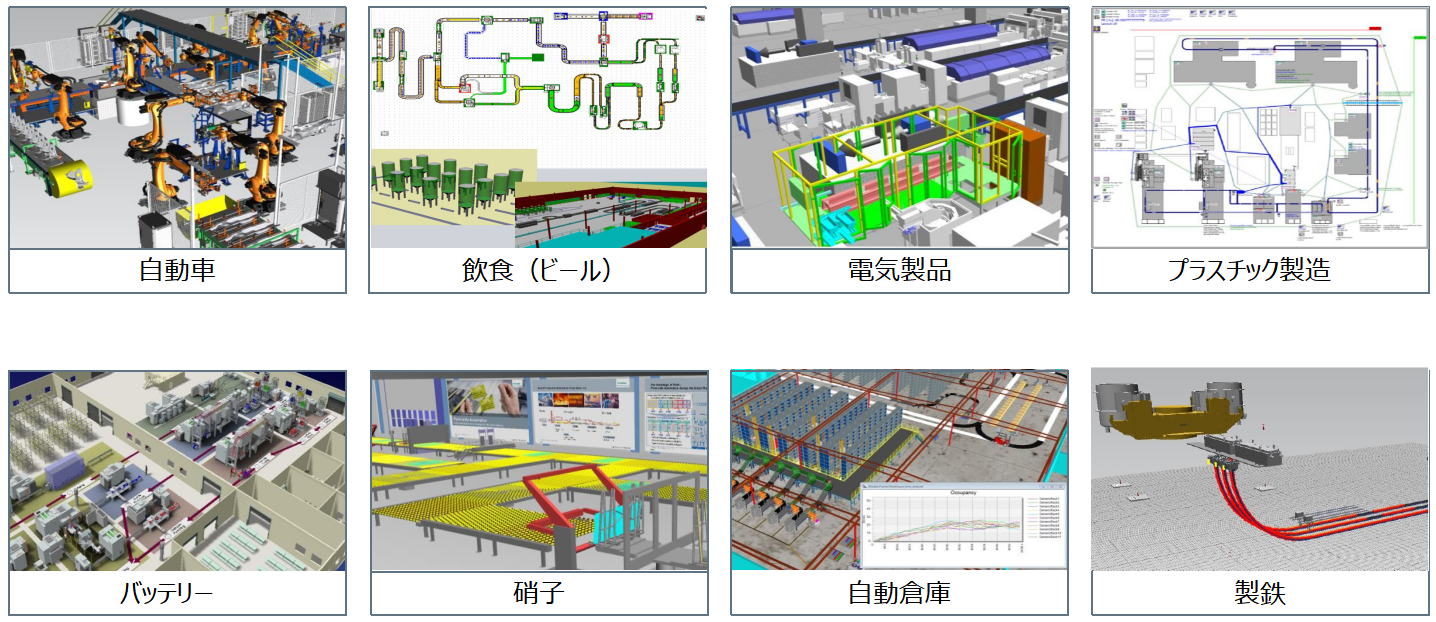 |
|
◆明確な導入効果◆ 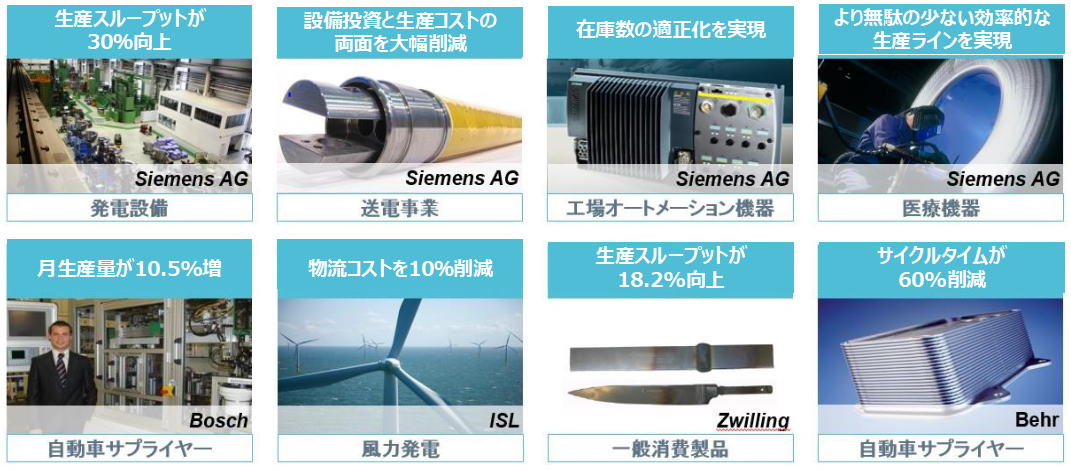 |
・VDA(ドイツ自動車工業会)標準ツール
・2005年にEvent Controlled Simulationの分科会設立により、Plant Simulationが
標準ツールとして認定され、シミュレーション適用を促進
・欧州自動車メーカなどで作成されたオブジェクトを共通ライブラリとして整備
・主要自動車メーカーを含む600社以上が参加 |
|
|
|
|
|
|
|
|
|
|
|
|